Gas Production Optimization
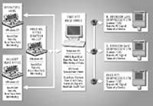
- The three compressor sites covered the entire system and there was a minimum requirement for equipment
- The three compressor sites were linked by an existing microwave communications network
- Remote monitoring would reduce the number of long trips from one end of the system to the other resulting in an immediate and significant time savings
- Remote monitoring eliminated the need for evening and night shifts allowing for more productive personnel, time and task management
To some extent the installation of this telemetry system was a pilot project for N/Acidental and therefore cost was a significant factor in the consideration of each component. For this reason a PC based Windows platform was selected along with a variety of commercially available software applications. A Human-Machine Interface (HMI) package, Wonderware's InTouch, provided the real-time display of compressor and measurement operation information. This package was designed after consultations with field operators and as a result, it displays both compressor and metering facilities as they exist in the field (i.e., the compressor monitoring view uses color coding to more easily differentiate between the various stages of compression). The company's ScanBase, a gas measurement data management package, allows operator to view, edit and generate monthly volume reports while maintaining a complete audit trail of historical information.
In this implementation, finalized measurement data is exported to Microsoft Excel, a spreadsheet package used to generate daily production reports. ReachOut's Remote Control package is used to monitor the system from PCs installed in the operators' homes, at the regional office 300 miles away, and at the corporate office in Calgary.
Hardware
The hardware in the field centers on the company's Scanner 1130 RTU. At each of the three field sites, a Scanner 1130 is used to monitor sales gas, fuel gas, and the SaskEnergy receipt meter. To accommodate the additional I/O requirements of compressor monitoring, a remote I/O signal telemetry device was used to allow various suction pressures, discharge pressures, temperatures, and the compressor speeds to be transmitted via Modbus to the central host located at For Pitt. Both measurement (Scanner 1130) and compressor data is collected on an hourly basis through a private microwave telephone network and shared with other alarm and safety systems.
System Features
The Scanner RTU and the remote I/O signal telemetry device communicate via distinctly different protocols. To accommodate transmission of historical measurement/production accounting information (not supported by Modbus) the Scanner used its native ScanCom protocol. The remote I/O signal telemetry device communicated via Modbus. Two DDE servers reside at the host each communicating from separate serial ports on the PC.
Both of these DDE servers, ScanDDE and Modbus DDE, provide data for the single InTouch HMI application in a seamless manner. In the field, ScanCom and Modbus are broadcast to both devices, these devices automatically recognize and respond only to their appropriate polls. This required the use of a serial multiplexer and illustrates that two protocols can reside on the same network without data collisions.
The private microwave telephone system was originally installed to provide voice and alarm callout services. Adding the Scanner and remote I/O signal telemetry device required the use of a telephone multiplexing device to receive calls and route them to the appropriate port based on numeric codes trailing the phone number. N/Acidental's operators had minimal experience on PCs and were originally intimidated by the new automation system. To assist in the transition to the computer age, they were each provided with PCs in their homes, justified by the fact that it allowed them to remotely monitor the entire system in the evening and on weekends. Intangible benefits (familiarity and confidence) came from the extra time operators had at home to use other applications on the PC. New skills were eventually transferred back to the workplace- increasing productivity.
System Benefits
The greatest benefit N/Acidental has derived from the system is the reduction f trips to each of the remote compressor stations. The former procedure required that an operator travel a minimum of 40 minutes each way simply to document compressor status; this information is now available immediately and from the comfort of the field office. Operators can now plan the day's activities around other maintenance or production optimizing activities.
The second major benefit gained from the system is early notification of production problems in the field. In the past, a well could freeze off and it might be a whole day before an operator would recognize and rectify the problem. Now, with data updated every hour, operators are alerted to problems immediately and can get production back on-line quickly.
This system is an excellent example of an effective implementation of remote telemetry equipment that fits within a tight budget and still delivers solid results.
<%=company%>, 900 S. Turnbull Canyon Rd., City Of Industry, CA 91745. Tel: 626-961-2547 (Ext. 532). Fax: 626-961-4452.