Paragon gets Williams Canyon Station contract
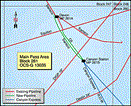
By Dev George, Houston
Paragon Engineering Services, Inc. says it has been selected by the Williams Company to assist in the development of a US Gulf of Mexico shallow-water platform that will accept deepwater production from remote subsea wells in up to 7,200 ft of water—representing the Gulf's deepest subsea development to date. Production of some 500 million cf/d of gas from the subsea wells is expected by summer 2002.
Newbuild facilities for a project known as Williams Canyon Station include an innovative, cost-effective system for ensuring the flow of the deepwater production to the shallow-water platform. As part of the development strategy, Paragon is performing project management, engineering, design/drafting, procurement, and fabrication inspection for the new platform.
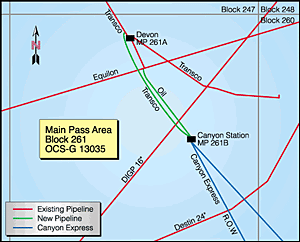
Alan Armstrong, vice president of gathering and processing for Williams' midstream operations, says Paragon and others along the Gulf Coast are participating "in a landmark project."
"Williams' Canyon Station positions us to be one of the largest independent service providers in the deepwater Gulf of Mexico. We're also designing our infrastructure and logistics to accommodate other prospects that may be developed in the East Breaks corridor," said Armstrong.
To solve the significant challenge to the Williams fast-track project of flow assurance to the shallow-water platform, Paragon says it has developed a process for the effective recovery and reuse of chemical methanol as a hydrate inhibitor for the project, which makes the project viable while helping to advance industry's deepwater development capability.
"The use of methanol and its recovery are essential to the project's economic viability, with significant operating cost savings anticipated," said Paragon's Hickman Brown.
The Williams Canyon Station project includes the effective storage, regeneration and distribution of some 1,900 b/d—or about 55 gallons per minute—of methanol. If the methanol were not recovered, Paragon estimates that the operator would have a cost impact of US$60,000 per day to successfully produce the 500 million cf/d of gas from the deepwater subsea wells.
Brown explains that the recovery process, as designed by Paragon, will allow Williams Energy to recover about 80-90% of the chemical for re-injection.
Industry use of methanol in deep cold waters is a critical tool for inhibiting the formation of hydrates, which can block production flow. Operators have used nominal amounts of methanol for many years to inhibit hydrates; however, its use on the Williams project represents an industry innovation for its expanded application and reuse.
The produced methanol will be used in the development of nine subsea wells in three deepwater fields: Aconcagua, Camden Hills, and Kings Peak. The subsea wells are located some 55 miles south of Williams' newly proposed shallow-water platform. The owners of the three fields—TotalFinaElf E&P USA., Marathon Oil Company, BP, Pioneer Natural Resources USA., and Mariner Energy, Inc.—have already approved the Canyon Express project to develop the gas-gathering system and infrastructure, which will tie back the deepwater wells to the Williams Canyon Station host platform in 299 ft of water. A 110-mile closed loop 12 ¾-inch diameter pipeline will gather production from the wells to Williams Canyon Station host platform.
"Tie back of the subsea wells to the host platform presents technical challenges, as hydrates could plug the line at any point. Equally significant is the 7,200-foot water depth, where temperatures below 40 degrees Fahrenheit can cause hydrates to form at the wellhead," said Frederik Rijkens, project manager of Canyon Express.
Brown adds that a 50/50 mix of methanol and produced water injected into the well will effectively inhibit the formation of hydrates to ensure gas flow. The methanol recovery process will have a design capacity of the 3,000 barrels per day of inlet fluids: 1,900 barrels per day of methanol and 1,100 barrels per day of water. The process involves separating the gas and produced water while boiling off the methanol for recycling. Upon regeneration, the methanol is 95% pure.
The Williams Canyon Station design calls for a four-pile, four-legged production platform destined for Main Pass Block 261. The topsides production deck is estimated to weigh 3,500 tons.
The jacket is scheduled for installation in summer 2001, with the deck to follow in spring 2002. Following jacket installation, Canyon Express will begin installation and testing of the umbilical to ensure its operability.
To facilitate the fast-track process, Williams requires a concurrent facilities design-and-build effort. Paragon will design the deck using the 3D Plant Design Management System (PDMS) to facilitate early resolution of design clashes and to improve operability and safety through better anticipation of hazards.
The engineering effort includes topsides system design for compression and separation facilities, water treatment, instrumentation and utilities, including termination and connection for power and control systems to the umbilical bundle for the subsea control center.