Tech Talk: Liquid Levels and Density
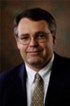
By Andrew W Sloley
Case histories with DP cell problems Differential pressure (DP) cells are the most often used level measuring device in the process industries. Differential pressure cells measure the pressure difference between two points and send a differential pressure reading to the plant control system. Typically, DP cells are rated in inches of water equivalent. Standard ranges include 0 to 20, 0 to 50, 0 to 100, 0 to 200, and 0 to 500 inches of water differential pressure.
The control system converts the DP cell reading into a liquid level based on an assumed specific gravity inside the vessel. Levels based on DP cells can err for different reasons. Previous columns have covered many reasons DP cells or sight glasses can give false readings. This column covers some case histories of specific DP cell problems.
Cryogenic unit with two operating modes
The first case involves a cryogenic field extraction unit that had two possible operating modes. The first mode was an ethane rejection mode where ethane was sent overhead (Figure 1). The second mode was an ethane recovery mode where the main tower switched to a demethanizer operation. The overhead product was methane and lighter and the bottoms product was ethane and heavier (Figure 2). The recovered liquid (tower bottoms) was sent to a separate plant that segregated the liquid stream into consumer LPG and petrochemical feeds.
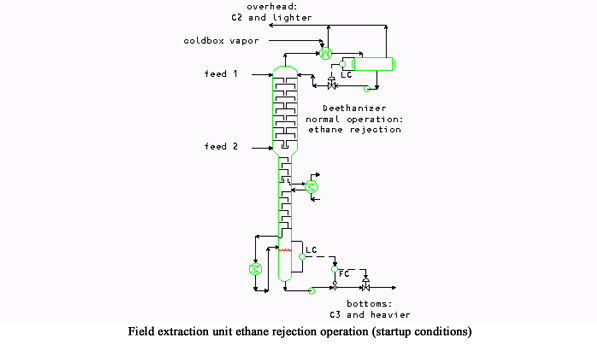
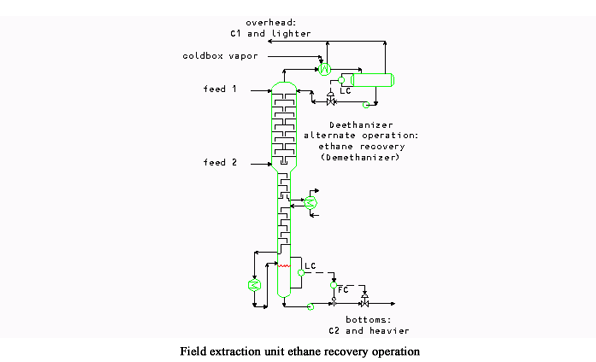
The plant started up in the ethane rejection mode successfully and operated there two years. After downstream facility modifications were made, the plant shifted into the ethane rejection mode. Tower problems occurred immediately. Major problems were intermittent flooding of the tower and inability to effectively control coldbox heat integration.
Field troubleshooting identified the culprit as changed densities in the tower. The ethane recovery mode had lower liquid densities. The lower liquid densities inside the tower caused ‘measured' liquid levels to be lower than the actual liquid levels. Normal tower boot liquid level variations caused liquid back-up into the reboiler return line (Figure 3). Normal overhead drum liquid level variations created liquid entrainment into the overhead vapor (Figure 4) going to the heat integration in the coldbox. The problem was especially acute in the overhead drum
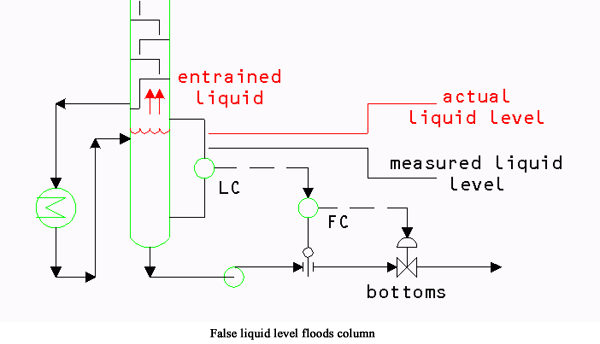
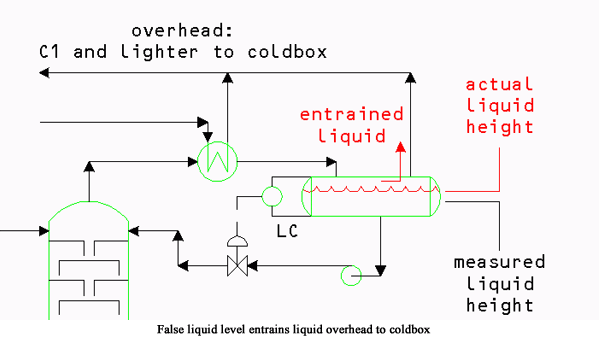
Calibrating the liquid level measurement for the new densities immediately corrected the operating problems.
Water hold-up causing level problems in overhead reflux drums
Many drums in hydrocarbon systems have water boots and separate water levels controllers. Typical services that have these on overhead drums include atmospheric columns, coker main fractionators, visbreaker atmospheric columns, and fluid catalytic cracker (FCC) main fractionators, among others.
On one FCC main fractionator, a fouled water level measurement resulted in pump cavitation, seal problems, and increased maintenance costs. Figure 5 shows the FCC main fractionator overhead drum and level control system.
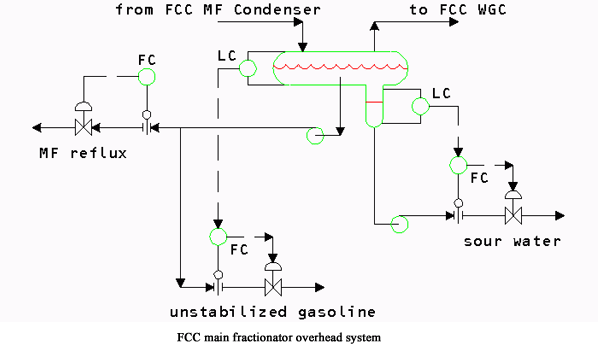
Immediately after a turnaround, the FCC started up without problems. However, after several weeks of operation pump seal problems on the reflux pump became common (Figure 6). Field troubleshooting quickly identified that the pump was cavitating. The initial conclusion was that the net positive suction head (NPSH) available was insufficient. This was puzzling because the pump had always worked before. An alternate idea proposed at this point was that the pump was damaged, creating a need for a higher NPSH. One pump of the two parallel pumps in the service was pulled and inspected. No apparent reason for NPSH problems was found with the pump. Design of the piping from the drum was checked. Again, no source of NPSH problems was found.
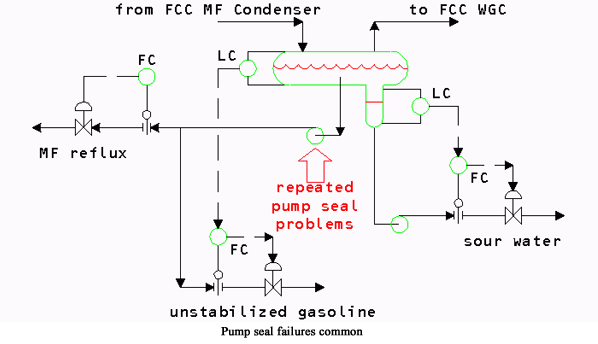
Over time, the new operation was accepted as normal. However, the situation continued to nag on some of the operators involved. While on site for operator training, the author was asked about this problem and a new troubleshooting effort started. Field data was gathered and compared to operating data. One suspicious observation was immediately obvious. The water level measured in the drum never seemed to vary. The connections to the water level instrument were blown out and the instrument placed back in service. The measured water level immediately jumped from 54% of range to 100%. The water level was above the upper water level tap. A plug in the line to the water level instrument had blocked the instrument at 54% of range (Figure 7)
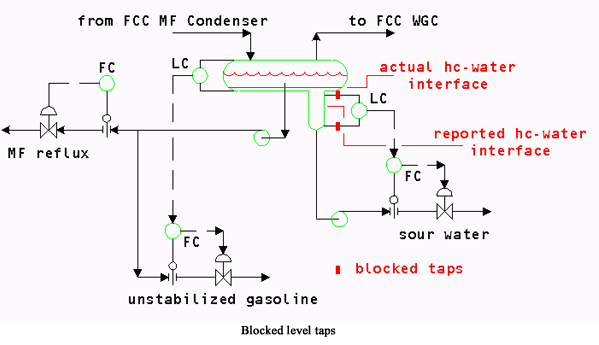
Actual water level varied down to nearly zero to up to the internal draw-off pipe to the unstabilized naphtha pump. Two problems were damaging the pump. First, water density is much higher than the naphtha density. The reported naphtha level in the drum was much higher than the actual naphtha level. Calculations showed that under some conditions the flow to the pump could be cut off entirely (Figure 8). At other times water ended up in the pump suction (Figure 9). Sudden water slugs to the pump dramatically increased power load and caused pump damage.
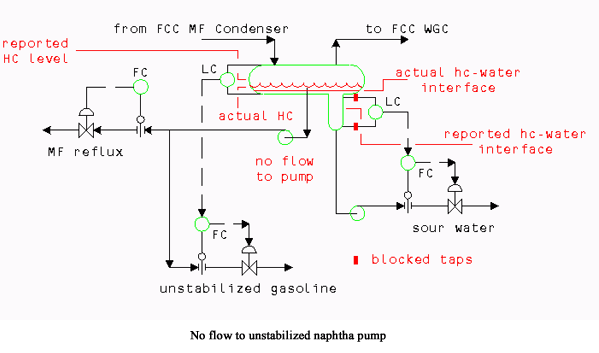
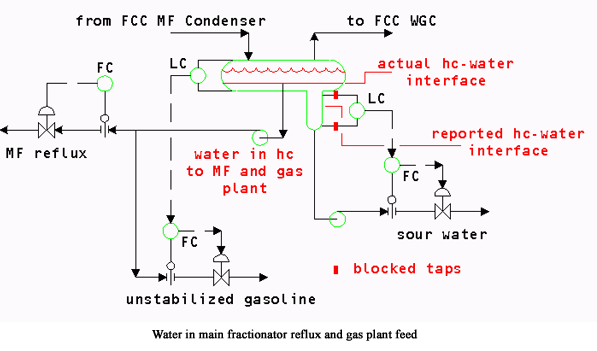
Review of operating records showed that at the same time pump seal failures increased, gas plant operation became less stable. The water in the unstabilized naphtha increased water entrapment in the gas plant absorber-stripper and increased propylene losses (Figure 10). The problems, seemingly unconnected, had the same cause, a single level instrument giving incorrect readings. Supporting evidence came from trends in main fractionator pressure drops. The main fractionator pressure drop had been gradually rising. Water in the main fractionator reflux vaporizes inside the fractionator and deposits solid salts (Figure 11). The salts plug trays and packing, increasing pressure drop.
Unit operation substantially improved with the level instrument back in service correctly.
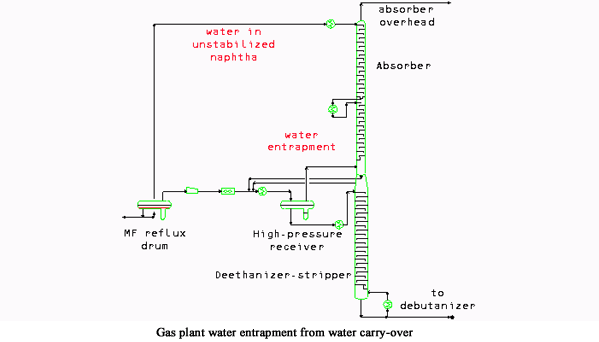
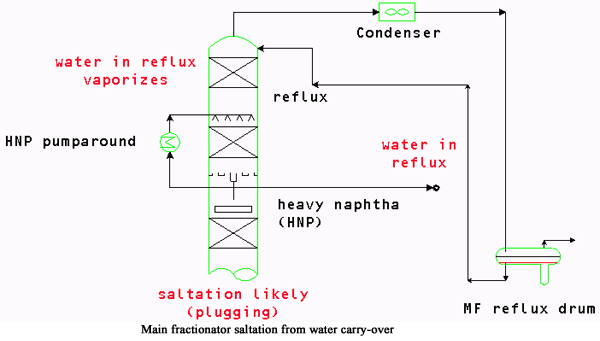
About the Author
Andrew Sloley is a consultant in distillation and troubleshooting. He worked as a troubleshooter and consultant for Glitsch, Inc. from 1990 to 1995 and for an engineering company between 1995 and 1999. Previously, he worked as a process engineer in technology development and application for Exxon Chemicals. His experience covers a wide range of petroleum refining and petrochemical areas. He has authored or co-authored over 90 publications and conference papers. Papers have appeared in Oil and Gas Journal, Hydrocarbon Processing, Petroleum Technology Quarterly, Chemical Engineering Progress, Hydrocarbon Technology International, National Engineer, and others. Conference papers have included presentations at the National Petrochemical & Refiners Association, American Institute of Chemical Engineers, American Society of Mechanical Engineers, Japan Society of Mechanical Engineers, Chemical Engineers Australia, and others. He currently acts as a consultant to a variety of companies in the area of troubleshooting and distillation. Other current work includes both engineer and operator training for distillation operations, design, and troubleshooting. Sloley has a bachelor's degree in chemical engineering from the University of Tulsa, and is a registered professional engineer in the State of Texas. He resides in College Station, TX, and can be reached at asloley@distillationgroup.com or tel: 979-764-3975 (www.distillationgroup.com).