WPC: Thermal Deasphalting Technology Presents Wide Range of Refinery Applications
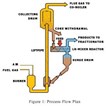
To meet this challenge, ExxonMobil and Lurgi have cooperated in a three-year development effort culminating in the start-up of the first commerical SATCON unit earlier this year. SATCON—Satellite Conversion—represents a novel mild "thermal deasphalting" process based on Lurgi's LR- Process and ExxonMobil's Fluid Coking experience.
The process principle, essential process characteristics, process background and current status of SATCON were presented at the 16th World Petroleum Congress in a paper entitled "SATCON: A Novel Process For Refinery Residue Conversion."
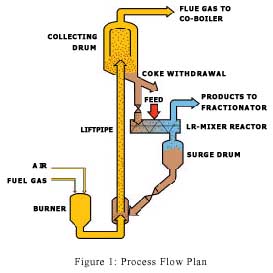
According to Dr. Hans Weiss, Lurgi Envirotherm GmbH, the technology is the culmination of a joint development program leading to technical readiness in 1996 at which time project development was initiated leading to the initial plant in Esso's Ingolstadt Refinery.
Conversion of petroleum residues (vacuum resid, bitumen, rock asphaltenes) is carried out in a unique, short-residence-time "LR-Mixer Reactor," which achieves a substantial reduction o f feedstock contaminants (heavy metals, CCR, N, S) at high liquid and low coke and gas yields.
The LR-Mixer Reactor includes two screws for mixing the feedstock with hot circulating coke. These screws clean each other and the reactor internals while they achieve plug flow of solids and minimum residence time of vapors.
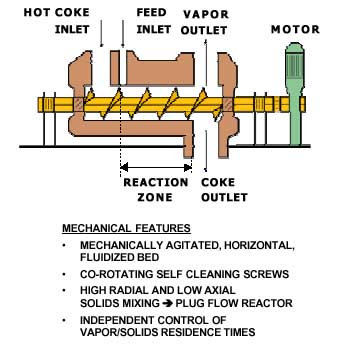
The overall mixer reaction can be described by two subsequent steps:
- Partial flash vaporization of feedstock
- Coking of remaining asphaltenes to additional oil, gas and coke.
The process thus can be compared to a thermal deasphalter with integrated asphaltene coking. There are a wide range of possible refining application scenarios, including resid pre-treatment prior to downstream catalytic processes that are sensitive to contaminants, upgrading of low value residues such as solvent deasphalter rock, etc.
Pilot plant units are in place in Lurgi's and ExxonMobil's process research facilities. These facilities permit feedstock testing for specific applications and permit evaluating enhanced technology features as part of a continuing R&D program.
Start up of the first commercial unit with an approximate capacity of 8,000 bpd at Esso's Ingolstadt, Germany, refinery is in progress.
Other authors of this presentation are John F. Pagel and Mitchell Jacobson, both of ExxonMobil Research and Engineering (Florham Park, NJ).
For more information, contact the World Petroleum Congress, www.wpc2000.com.
By David Nakamura