Yokogawa, Shell Form Advanced Process Control Alliance
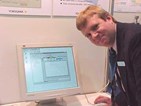
Although Yokogawa Electric Corp. (Tokyo, Japan) is a leading process control vendor, it has generally focused on smaller chemical and process industry facilities. That is going to change.
Yokogawa chose ISA '99 to announce that it is forming an alliance with Shell Global Solutions, part of the Royal Dutch/Shell Group, to market Shell's advanced process control (APC) systems. Shell's ten- year-old APC is designed for refineries and petrochemical and chemical plants.
According to Yokogawa, Shell's APC has proven itself at more than 430 Shell facilities worldwide. Applications range from styrene EO/EG, and petrochemical production to distillation and FCC operations. The company says the software provides superior stability and uptime.
Challenge the Leaders
The alliance gives Yokogawa both a product and an installed customer base with which to challenge the APC leaders. These include Aspen Technologies' DMCplus, Honeywell Hi-Spec Solutions' Profit Controller (formerly RMPCT), and Simsci's Connoisseur.
While the companies have not yet finalized the deal, both say negotiations are in an "advanced stage." Both Shell and Yokogawa personnel jointly displayed the technology at Yokogawa's booth at ISA '99.
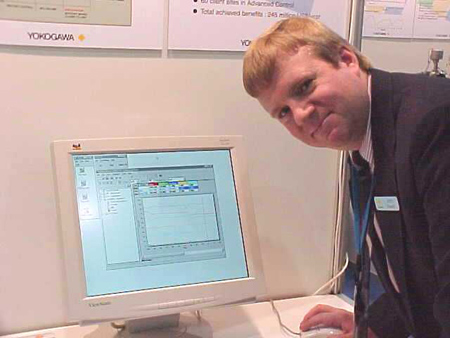
Under the proposed agreement, Yokogawa will sell Shell's APC through its global marketing channels. The two companies will jointly design, install, and support the technology. They will also collaborate on future APC development.
APCs are middle-level systems that connect a plant's distributed control system (DCS) to a higher-level manufacturing execution system (MES). According to Yokogawa, chemical makers and refiners increasingly want vendors to deliver integrated DCS and APC systems. The company is a major DCS vendor and also supplies enterprise resource planning and MES systems.
Yokogawa Electric Corporation is setting up a solution center in Singapore to serve markets in the Middle East, Asia, China, and Australia. It already operates similar centers of excellence in Japan, the United States, and Europe.
SMOC and AIDA
Yokogawa's deal with Shell Global Solutions involves four separate technologies: SMOC (Shell Multivariable Optimizing Controller); COAST (Control Application Standards); and RQE (Robust Quality Estimator); and AIDA (Advanced Identification and Data Analysis).
SMOC represents the heart of the technology. A model-based system, it uses mathematical algorithms to achieve multivariable predictive control, improve process stability, and optimize plant economics.
According to Yokogawa senior advanced control engineer John Blaesi, "SMOC is similar to AspenTech's DMCplus APC, but is more robust." Yokogawa claims SMOC achieves the highest uptimes in the industry.
One reason for its robust predictive behavior over time is its use of "gray box" models. "DMCplus uses a black box model, which looks at the flow in and the analyzer out, then builds a model," explains Shell advanced control and optimization head engineer Barry Cott. Since the actual process that changes input to output is unknown, it's referred to as a black box.
"SMOC looks at those variables, but we also take into account pressure, temperature, and some other variables. We don't try to model the entire process, just some key variables. Because we know something about the process, we call it a 'gray box.'" He says the gray box approach improves uptime and plant efficiency.
SMOC embeds in the DCS and does not require special interface software or duplicate databases. The SMOC online controller supports Honeywell AxM/TPS, Foxboro IA, and Yokogawa CS DCS systems, and Setcon, Info Plus, Pross 2, and OSI PI process computers.
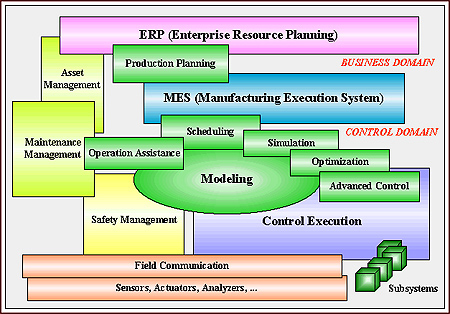
SMOC comes with AIDA, a software package used to estimate linear dynamic process models. The models feed into PC-SMOC, Shell's Windows-based offline controller design package. It lets engineers design, build, and test SMOC controllers offline. PC-SMOC then uses AIDA linear models (or models generated with a graphical model builder) to simulate plant behavior. This allows engineers to tune, test, and optimize the model before using it in SMOC's online controller.
Quality and Standards
Yokogawa's new offering also includes Shell's Robust Quality Estimator (RQE), which Cott describes as a "best practices quality toolkit of advanced algorithms). RQE includes a Windows-based offline tool to analyze data and model inferred measurements.
The online tool then uses the model to predict critical chemical properties or process variables that cannot be measured directly. These might include refinery reaction products or product quality estimation in multidraw fractionators.
Engineers generally use RQE in combination with either an online analyzer or laboratory measurement system to provide process feedback and automatic model update.
RQU is part of COAST, a library of best-practice standard advanced control modules. The library includes:
- Shell surge volume control (SSVC). Minimizes feed flow changes on downstream units by optimizing surge vessel capacity. A nonlinear controller, it allows operators to enter minimum, maximum, and steady state level targets.
- Furnace coil balancing. Balances the outlet temperatures of up to 16 furnace coils by adjusting coil flow setpoints. Takes into account passes to be balanced, wind conditions, exact total flow control, and tube skin temperature constraints.
- Column tray loading. Calculates distillation column loading conditions. Works with sieve and valve trays, and covers open-slot and seal pans.
- Constraint pusher. An online closed-loop single-variable optimization technique. It pushes a single variable in one direction until process constraints kick in. Can be used to maximize unit throughput or minimize column pressure.
- Pressure-compensated temperature. Uses a modified Clausius-Clapeyron equation to derive a tray temperature corrected for pressure variations. Used to control distillation cut points.
- Other modules. Other modules include uptime monitoring of control applications, online measurement validation, and online signal noise rejection.
Foundation Fieldbus
Yokogawa also chose ISA '99 to announce it will team with Dresser Equipment Group, Inc., a Halliburton Co. subsidiary, to develop and market Foundation Fieldbus products, integrated systems, and management tools. The first product from the two companies will be a new Foundation Fieldbus-compliant positioner.
The alliance will establish a professional team that will take on single- source responsibility for purchasing agreements and projects. The goal, say the two partners, is to reduce customer enterprise-wide costs, compress project schedules, and minimize technology implementation risks.
For more information: John E. Blaesi, Senior Advanced Control Engineer, Advanced Automation Div., Yokogawa Corporation of America, 401 S. Dewey, Ste. 401, PO Box 848, Bartlesville, OK 74005. Phone: 918-337-0918, Ext. 237. Fax: 918-337-0968.
Or: Barry J. Cott, Head Engineer, Advanced Control Manufacturing/Advanced Control and Optimization, Shell Canada Products Ltd., 3655 36th St. NW, Calgary, AB T2L 1Y8, Canada. Phone: 403-284-6646. Fax: 403-284-6662.
By Alan S. Brown